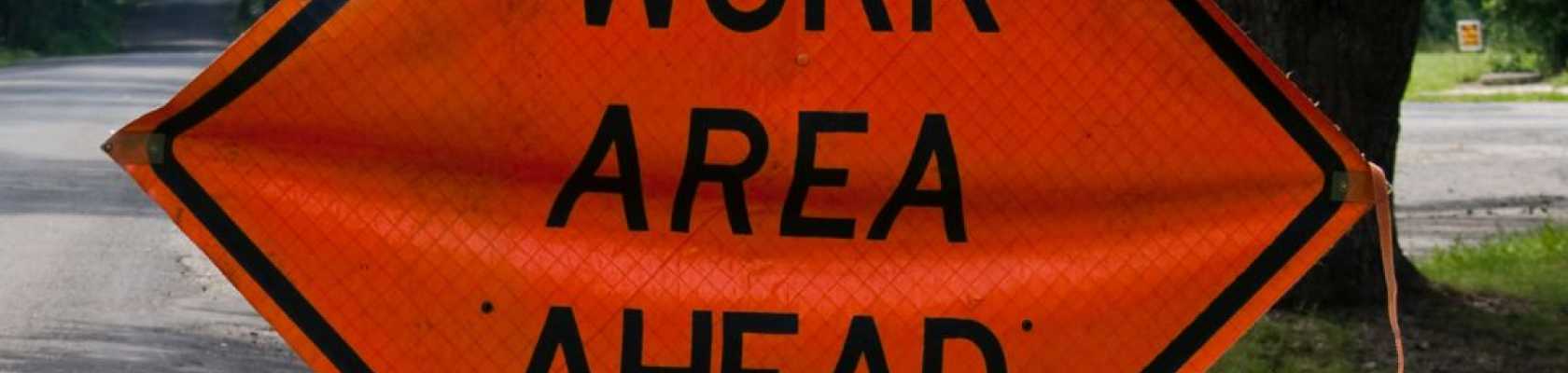
When a park or facility has a maintenance issue, time matters. Minor issues often become big problems if they are not addressed promptly.
Establishing a work order system is one of the best ways to identify and fix issues efficiently. Work orders play a fundamental role in most maintenance departments. When the system operates well, maintenance managers and their teams stay organized, prioritize appropriately, and help prevent disruptions in workflow or programming.
This article gives an overview of work orders and why they’re important. Then get some tips about making your work order system more effective.
What is a Work Order?
A work order provides information about a task that needs completion. The task could be a repair, replacement, or routine work. Usually, a work order is a piece of paper or a digital file distributed among the appropriate people in the maintenance department.
An effective work order should be clear, specific, and detailed. Precise and concise details avoid confusion or misinterpretation. The person completing the work order should know exactly when, where, how, and what needs to be done.
Work orders also help address future issues. Recording information about work completed provides a clear “paper trail” of the asset’s maintenance history.
Is a Work Order the Same as a Work Request?
A work request is different from a work order. A work request begins the work order life cycle, which we will touch on shortly.
Generally speaking, a work request gets submitted to the maintenance department.
Then, the maintenance supervisor or asset manager reviews the work request. When a work request is approved and assigned to a person or crew, it becomes a work order.
So, in many cases, a work request is submitted by someone outside the maintenance department. It may be somebody that noticed something during programming. Or an issue reported to the front desk staff by a visitor.
Sometimes, however, maintenance staff will notice something outside their scope of expertise or that they must wait to address. They will create a work request or work order depending on their authority.
Benefits of an Established Work Order System
Most maintenance departments have some type of work order system in place. Sometimes they are very organized and efficient. Other systems may seem overly complicated and redundant, which ultimately slows the workflow.
And then there are the departments that don’t have anything in place. They either operate almost exclusively reactive, or they’re experienced enough to go on gut feelings and their memory.
Hitting that sweet spot where the work order system moves things along without causing too many kinks in the workflow is ideal. And when that happens, maintenance departments and agencies benefit by:
Creating A Centralized System
Forget post-it notes left on a messy desk or an email in a crowded inbox. Everyone understands the process when every work request and order moves through the same system. Systemized work orders have a higher chance of being noticed.
Reducing Paperwork
The less paperwork, the better, right? Plenty of other things need to get done. Why spend extra time on a form that’s complicated just to be complicated?
The quicker someone can report something and get it through the system, the better.
Plus, a user-friendly system makes reporting an issue easy. And let’s face it, the simpler the process, the more likely it will get done.
Budget and Plan More Accurately
An organized work order system allows you to pull data that could be invaluable when arguing things like--equipment replacement, staffing issues, and the operating budget. Ideally, your work order system will only collect valuable data for your team and the agency. If it’s just collecting information that won’t ever get used, it’s slowing down the process.
Easy Access to Information
Once a work order is completed and recorded, that information should be easily accessible. Convenient records give the ability to see how things got repaired before, the frequency of issues, and much more.
If everything gets stuffed in a file cabinet, hours may be wasted looking for instructions, maintenance history, and other critical information. And, honestly, there are not a lot of extra hours to spare--especially in the growing season.
More parks departments and municipalities opt for digital records to free up space and make the information easier to access.
Stay in Compliance
If you have records of it being inspected, repaired, and replaced, you’re covering all your bases for risk management and liability issues. Plus, records of repairs and maintenance may help with warranties.
The Work Order Life Cycle
Feeling inspired? Here’s a brief look at a typical work order life cycle that you can compare to the processes you have in place.
- Issue Identified: Someone sees something leaking, broken, wobbly, or otherwise not normal.
- Work Request Created: The person who notices the issue sends a request to the maintenance department to address the problem.
- Maintenance Supervisor Approves and Assigns: The maintenance supervisor reviews the issue and determines who, what, when, where, and how to resolve the problem. A work order is created, scheduled, and given a priority level.
- Work Gets Completed: Assigned staff completes the repair, replacement, or maintenance.
- Document Work Performed: Once finished, the staff records any relevant information about the work completed, like materials used, the time it took, or the steps to fix the issue.
- Data Stored for Reporting and Analysis: Records get stored for future reference.
Now that you see the process ensure that your work order form has all the necessary information to convey what work needs to be completed.
What to Include In A Work Order Form
Certain essential information should be included in every work order. Work orders missing appropriate information could lead to confusion and delays in tasks completed.
Here are some essentials most work orders need.
- Name of Person Requesting Work: Someone to refer to if the person completing the work order has any questions.
- Location of the Issue: The exact spot that needs attention. If necessary, find a way to specify sub-assets to avoid confusion.
- Due Date/Time: Give a deadline or schedule a specific time to handle the issue.
- Who Authorized the Work: Allows the assigned staff to know where to go if there are more issues or questions.
- Who Performs the Labor: Addresses who is responsible for completing the work.
- Information About the Task: A clear, concise statement defining the task.
- How to Perform the Work: Provide any relevant, helpful information to help the assigned staff complete the task like any special tools, equipment, or supplies that need to be brought.
- Notes After Task Gets Completed: Assigned staff relays any important information regarding the task.
The specifics of your work order will depend on many factors, like the size of your agency, how you specify assets, how work gets routed, and agency-specific procedures.
Make sure your work order is as efficient as possible. Go through each item on your form. Determine what information is vital to the task getting completed. If it’s not serving a definite purpose, remove it.
Don’t make anything more complicated than it needs to be.
Once the fluff gets removed from the work order, give it a few test runs. If everything seems to be going smoothly despite the revised work order, you’ve probably just saved everybody a bit of time.
Digital Work Orders
Another way many parks and recreation agencies began saving time was with a digital workflow.
Someone in an agency can spot an issue and report it from a web-enabled device. That work request immediately gets routed to the appropriate person. The supervisor signs off on the work, and it alerts the assigned staff. The assigned staff completes the work as scheduled. After the work is done, staff adds notes or images about the task. Once submitted, the records get stored digitally.
When someone needs data based on the work, it’s easily accessible through a maintenance management dashboard system.
As you can guess, once everyone is on board with a digital workflow, it saves lots of time and unnecessary steps. Some software, like computerized maintenance management software (CMMS), can automatically generate a work order when issues are noted during inspections and other predetermined times.
As more municipalities require data to back up their budgets, capital expenses, and more, a CMMS allows easy access to reports, data, and work history. Going digital seems more relevant than ever.