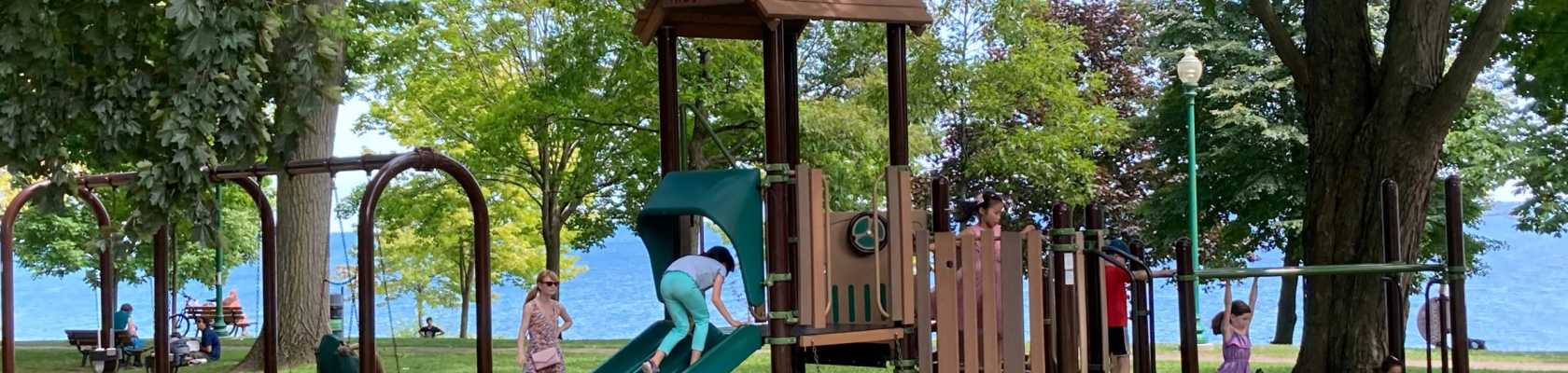
Playgrounds are a source of joy for families. It's an opportunity for children to get physical activity while their imaginations run wild. Many fond childhood memories occur in the playgrounds we work hard to maintain.
According to the United States Consumer Product Safety Commission, more than 200,000 children go to emergency rooms with playground equipment-related injuries annually. The PDRMA estimates nearly 40% of playground injuries occur due to ineffective inspections and maintenance. It's our responsibility to make sure these playgrounds are safe and secure for park visitors of all ages.
Regular playground inspections are not only a best practice; they are required by law. In January of 2000, federal regulations required all playgrounds to undergo safety inspections by qualified individuals.
Here are some inspection suggestions for the various areas of a park:
Parking Lots
Parking lots are where visitors first experience your parks. You want to make a great first impression by ensuring your parking lots are safe and well maintained.
Inspecting parking lots includes:
- Cleaning litter and debris
- No tripping hazards like fallen branches
- Empty trash receptacles
- Parking spaces and fire lanes are clearly marked
- Surfaces are even without large cracks or potholes
- Parking lot lights working properly
Playground Signage
This playground inspection area is often overlooked, but signage serves an important purpose. Make sure your park visitors know the park's name, rules & regulations, and suggested ages for usage.
Inspecting playground signage includes:
- Signs are securely & clearly posted
- Signage is free of graffiti
- Signs include the site's name, operating hours, age limits, and park rules
- Seasonal or event signage (when appropriate) is present
Paths Leading to Parks
Once your visitors get out of their cars and see the signs, they are ready to play. Make sure they safely navigate the sidewalks & paths leading to the parks.
Inspecting sidewalks & paths include:
- Removing litter and organic debris
- Checking for low hanging or fallen tree limbs
- Surfaces are even noting any cracks in concrete, trail erosion, or tripping hazards
- Path level flushes with playground surface
- Noting the presence of snow or ice
Playground Surface Materials
A majority of playground accidents involve falls. Properly installed and maintained playground surface materials can reduce the chance of significant injuries.
Inspecting playground surface materials include:
- Protective surfacing extends at least 6 feet in all directions from play equipment
- Surfaces around the playground have at least 12 inches of wood chips, mulch, sand, or peal gravel
- Check rubber playground surfacing for cracks, pits, or other tripping hazards
- Inspect fall areas for proper surface material depth and rake to fill in low areas
- Removal of litter, fallen branches, or other tripping hazards
Playground Equipment
Playground equipment is designed for long-term use. However, usage, weather, and time cause wear & tear, parts to break down, and other playground hazards.
Inspecting playground equipment includes:
- Checking for litter and graffiti
- Warning signs are clearly in place
- Guardrails and barriers are securely in place
- No footings are loose, exposed, or cracked
- Proper movement of dynamic elements and noting any wear
- Inspecting for pinch points, rough edges, and cracks
- Clamps, rivets, and hardware are present and secure
- Check hardware that may cause injuries like protruding bolts or open "S" hooks
- Openings in guardrails, ladder rungs, etc., are less than 3.5 inches or more than 9 inches
- Wood surfaces are smooth
- No rust, corrosion, or peeling paint
- Tree limbs are more than 84" from equipment
This is not an exhaustive list, but it will give you a good foundation if you are developing or improving your playground inspections.
Creating a Playground Inspection Plan
Establishing a system for playground inspections ensures each of your assets gets inspected, maintained, and repaired promptly. It's a system that benefits everyone:
- Park visitors are safer.
- Maintenance crews know what to look for at the sites.
- Crew leaders handle minor problems before they become something significant.
- Management has records to help make informed decisions.
When creating or improving your existing playground inspection plan, consider these questions:
Who will be completing the inspections?
Ideally, inspections should be consistent. Achieve consistency in two ways: thoroughly training staff on playground inspection procedures and using the same staff to conduct the checks each time.
You may want to schedule frequent quick checks (looking for trash or hazards) as well as in-depth inspections (examining all aspects of a playground).
What staff you will use for each? In-depth inspections may require someone with special training in playground safety. Quick checks can be completed by most crew members.
How often should park inspections take place?
There isn't a single correct answer about how often park inspections occur. More detailed assessments depend on the recommendations of the playground equipment manufacturer, season, park usage, and programming using the playground. Ideally, you want someone doing at least a quick check daily or every other day.
Ultimately, scheduling inspections will depend on your assets, workflow, and perceived need. In this case, less is more may not be the ideal answer.
What are the inspection procedures?
Create a standardized way of completing inspections. For example, have paper checklists in each of the vehicles. Then the crew has access to the paperwork while in the field.
An individual completes an assigned inspection by filling out the checklist. Once finished, the list gets returned to the office for filing or adding to a database. Back at the shop, the crew member will create work orders for any issues observed.
Some parks & recreation departments are switching to maintenance software. This software allows staff to complete an inspection checklist using a tablet or cell phone. The information gets immediately stored in the cloud-based software for easy access and communication. (No more file cabinets filled with old inspection checklists).
Maintenance software helps improve efficiency. Managers can make real-time changes to inspection assignments, schedules, or tasks and quickly alert the crew. Deficiencies during inspections automatically draft work orders. Reports can be instantly generated for staff and management meetings.
Find the procedures that work best for you and your team. Once a solid playground inspection routine gets established, you'll notice an improvement in park safety, appearance, and maintenance.