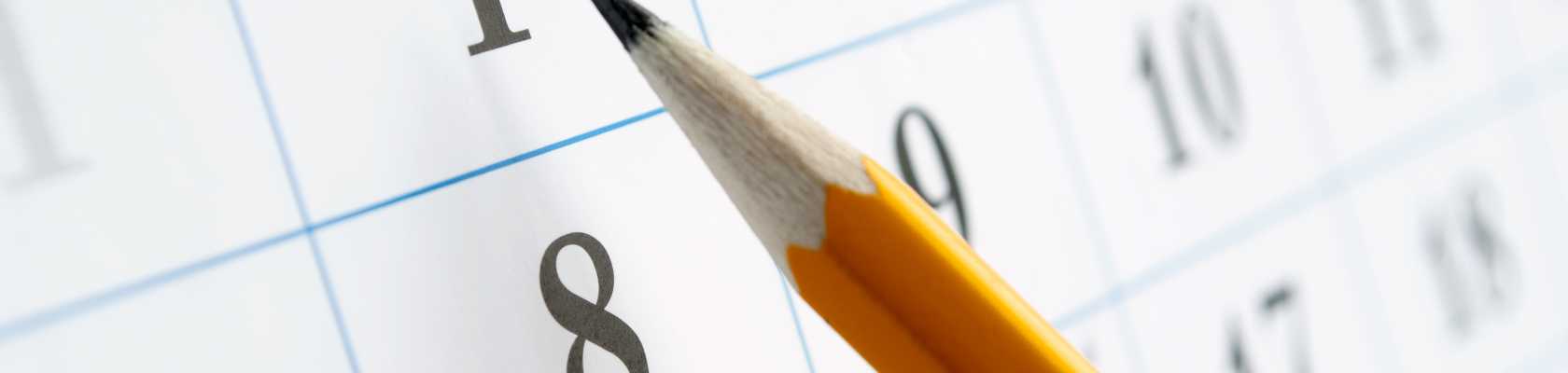
One of the best ways to make sure your crew stays on schedule is by ensuring everything works properly. Vehicles, building systems, tools, and other equipment need to be inspected and maintained routinely to ensure they work when you need them.
Integrating preventive maintenance tasks into daily and weekly work routines isn’t always easy--especially during busier seasons. Ignoring preventive maintenance, however, can cause much bigger scheduling problems down the line.
In the final installment of this series (see Part 1 and Part 2), we are going to give you some tips and strategies to help organize and assign preventive maintenance tasks to keep your workflow running smoothly.
Developing a Preventive Maintenance System
It’s important to have a system of identifying, scheduling, and tracking preventive maintenance tasks. If you’re looking to create one (or tweak an existing one), here are some things to consider:
Identifying
Your crew is probably performing the obvious routine maintenance tasks now. But some things may slip through the cracks. Is a crew member going to remember a semiannual greasing or replacing a fan belt during your department’s busiest season?
Start by listing every preventive maintenance task for each system or piece of equipment. Remember, no task is too small--you want to prevent bigger things from happening later.
Next, determine the time it will take to perform each task. Factor in time for planning, travel, ordering supplies, cleanup, and record keeping. If you are unsure of the total time and manpower, your crew should start tracking this information once the scheduling system is in place.
Scheduling
Once you identify the tasks and how long they take, it’s time to schedule. There are different ways to do this--and every department probably has a slightly different version of it. Here are two of the more common ways:
- Reminder tabs file: Creating one card for each piece of equipment and list the types and frequency of maintenance required. Provide space next to each task to document when it was completed. Color-coded tabs are attached to the cards to indicate daily, weekly, etc., tasks.
- Frequency code cards: A different card is created for each preventive maintenance task required for a piece of equipment. These cards are also color-coded by frequency. This system requires more cards, but there’s additional space to document and share more information about the task.
For scheduling your crew, it typically depends on the personnel you have available and their knowledge and ability to complete the tasks. Some parks and recreation departments prefer using the area maintenance method--a specialist is assigned to a defined area.
Other departments find using a crew to cover a larger zone is helpful. The crew method can be useful when maintenance tasks require more than one person or someone with more specialized skills.
Both methods have their pros and cons. Ultimately, it will depend on your knowledge about the required tasks, available crew, and the resources of your department.
Tracking
If it’s not documented…it didn’t happen. Tracking preventative maintenance is just as important as scheduling it.
As we mentioned earlier, tracking will help you get a better idea of the time and manpower required for each preventative maintenance task. Tracking also allows the specialist or crew supervisor to report back on the work done, supplies used, and note anything out of the ordinary.
Carefully kept records allow you to track your assets, equipment, supply quantity, and more.
Parks & Recreation Job Scheduling
This series discussed the best practices for scheduling jobs, crews, and preventative maintenance. We tackled each subject separately, but, as you are probably well aware, all these aspects are integrated into your parks and recreation department.
Scheduling is a crucial aspect of running a parks department. And it could also be one of the most challenging.
Once a system is set up, it’s easy to oversee, evaluate, and make changes to schedules (and much more) when needed. This will save time, frustration, and the potential for missed communication. While it may seem like a big change for how a department operates…it’s also a logical change.