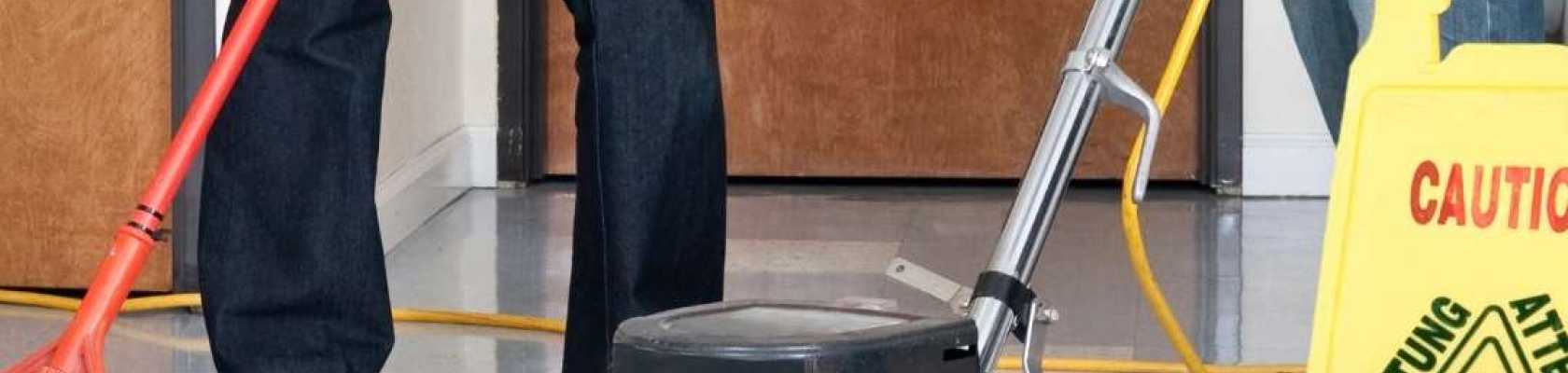
At some point, you will find yourself searching for new maintenance equipment. There is a lot of building maintenance equipment out on the market. How will you know what’s best for your facility?
It’s easy to get caught up in the moment while searching. The latest technology, newest innovations, or bargain prices may catch your eye. But, of course, you don’t want to buy something that may not be the right fit for your facility.
Before you hit the “add to cart” button, you should do a quick assessment to ensure the equipment is appropriate for your crew and your building’s needs.
Ask these questions before purchasing:
Who will use it?
When browsing catalogs or talking to a salesperson, it’s essential to know exactly who will operate the equipment.
You know this piece of equipment is necessary for your facility. Do you have the staff that understands how to operate it effectively? If not, will it make sense to have contractors come in and get the job done?
Is the equipment easy to use?
Complicated equipment requires extra training. Standardized equipment saves time. New staff with some maintenance experience probably know how to operate more standardized equipment, so less training is required for onboarding staff.
If your agency tends to have a high turnover of maintenance staff, you want to make sure the equipment is straightforward.
Is it safe for all operators?
Let’s face it, not everyone on your crew is created equally. Ergonomic features allowing adjustments to individuals’ varying sizes and physical abilities can prevent work-related injuries.
How often will it be used?
Will this equipment be used daily? Weekly? It’s it something your crew frequently needs to complete tasks?
Or do you plan on using it quarterly or annually? Then it may make sense to rent the equipment or hire contractors. Renting or using contractors also means you won’t have to worry about maintaining or serving the equipment.
Are replacement parts and servicing readily available?
These days, supply chain issues affect many industries. Getting replacement parts can be tricky. Waiting weeks for a part means tasks aren’t getting done. If you feel purchasing the equipment is your best option, you have to understand what goes into maintaining it.
Also, consider who performs the scheduled and preventive maintenance of the new equipment. Is there someone in-house that takes care of it? Will you need to hire a company to do routine checks and maintenance?
Calculating the total cost of ownership is just as important as the initial cost of the equipment.
Again, choosing standardized equipment can make maintenance and repair much more manageable.
Is there space to store the equipment?
Say, for example, you found a great deal on floor cleaning equipment. Parts are reasonably easy to get, and your on-site technician is familiar with maintaining it.
It seems like the perfect fit. That is until you realize it won’t fit into your facility’s supply room. Leaving it in an open space looks unprofessional and could pose a safety hazard.
Now you’re stuck with a great piece of equipment with nowhere to store it.
Does the equipment meet your agency’s Sustainability Plan?
Many parks and recreation departments are adopting sustainability plans to be more mindful of their impact on the community and environment. Choosing resource and energy-efficient products that align with these plans saves on operating costs and supports your agency’s mission.
Getting the Most Out of Your Investment
You found the right equipment. You have staff to operate and maintain it. It fits in storage. Great!
Now make sure a plan is in place to keep it running throughout its useful lifespan. Scheduling routine and preventative maintenance reduces the chance of equipment failures and workflow disruptions.
Software can help automate and track equipment maintenance tasks to ensure everything gets done to make your team’s newest “toy” work when needed.
Happy shopping!