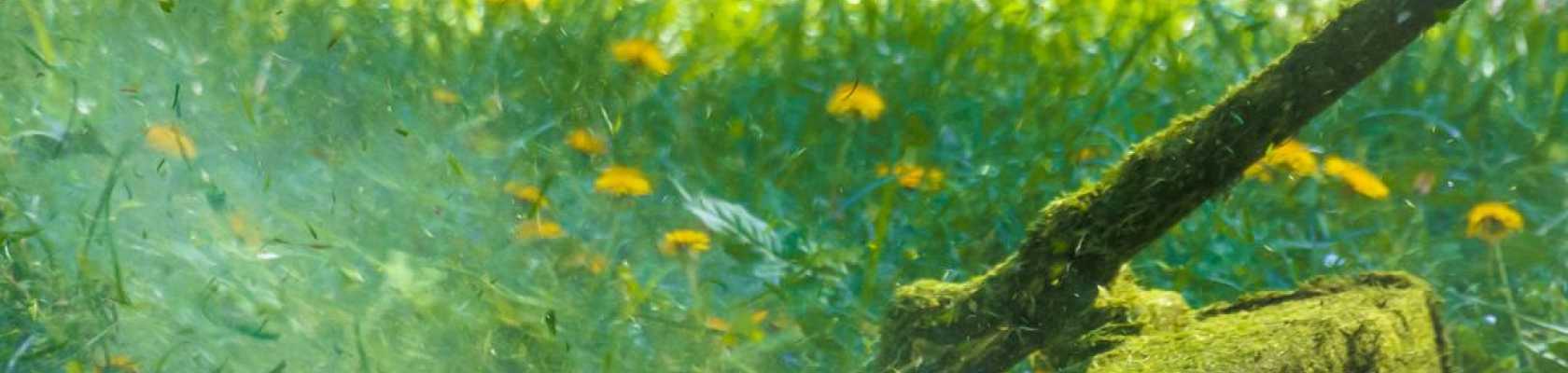
Do you know one of the best things about paperwork? When you find a way to reduce it.
That's the idea behind standing work orders. Creating standing work orders can save time and administration costs. But there are some things to consider and be aware of before adding them to your workflow.
Let's take a closer look at standing work orders, their benefits, and how to use them to your department's advantage.
What is a Standing Work Order?
A standing work order is a scheduled task you leave open for a particular time. When a job in the standing work order gets completed, an update gets put in the work order, but it doesn't get closed.
In contrast, a regular work order gets closed when the task or inspection is completed. The work order gets filed away. Sometimes data or information gets recorded with the work order to help with tracking and budgeting. When that task is necessary again, staff generates another work order.
Generally, the tasks in a standing work order are recurring, routine tasks. They may not be tied to a specific piece of equipment or asset. For this reason, keeping detailed records may not be necessary. Making new work order tickets each time creates unnecessary paperwork.
When are Standing Work Orders Used?
As a general rule of thumb, the tasks assigned in a standing work order generally take 15 minutes or less. They are often routine, mundane tasks.
In other words, a standing work order may be appropriate if it takes longer to create and close the work order than it does to do the task.
Examples of tasks in a standing work order include:
- Shop/garage cleanup
- Checking tools or safety equipment
- Cleaning mowing equipment
- Trainings or meetings
- Setup/Tear Down
- Minor, less involved inspections (checking playgrounds or trails towards the end of the day.)
The Benefits of Using a Standing Work Order System
The obvious benefit is less paperwork. Also, less opening and closing work order tickets all the time. Fewer work orders mean reduced administrative costs. If you still use a paper system for tracking work orders, it also saves space.
What are the Potential Problems of Standing Work Orders?
Sometimes those routine, mundane tasks add up. Too many standing work orders without a reliable tracking system could mean some start slipping through the cracks. Also, you may be creating gaps in your data that can affect accurate budgeting.
Systems help keep things straight. Without a way to track standing work orders, standing work orders may not get renewed when appropriate. Or the work orders continue for years--if needed or not.
What to Consider When Making Standing Work Orders
If you think you have an efficient system and receptive team, then standing work orders can help save some time and money.
When creating standing work orders, consider the following:
- How long will the standing work order last?
- What's the process of closing a standing work order?
- How will the work orders be renewed once closed?
- Does the agency need any data about the tasks in the order?
- What's the review and evaluation process to ensure the orders remain appropriate?
With a clear system, the standing work orders should run smoothly, and any data you need gets collected.
Other Ways to Save on Paperwork
Digital paper trails are easier to manage. Computerized maintenance management software (CMMS) helps organize, centralize, and automate task management, work order tracking, and more. Several types of CMMS software solutions are available with various features.
Ultimately, a CMMS's goal is to make you and your team's lives easier--not create more headaches with complicated software. When choosing a CMMS, it's important to consider who created it and if they are familiar with your particular industry.
Software developers that understand an industry's specific needs, make a CMMS that’s more intuitive in addressing those needs.
Industry-Specific Features
For example, we at Productive Parks included a "bucket task" feature in the software. The feature addresses the issue that sometimes you may not know which staff are available for any given day in the future.
Here's how it works: A maintenance manager or administrator creates a bucket task and gives it access to staff responsible for completing those types of tasks. The administrator also sets a date when it needs to get completed. Now, any approved staff member given could pull and complete the bucket task when they have time available.
Bucket tasks work great when the crew has independence and the authority to determine the jobs most appropriate for a given day. They are also helpful as a reminder for long-term tasks that may not be ready for scheduling but don't want to be forgotten.
This is just one of several ways we have developed a CMMS specifically for parks and recreation agencies.