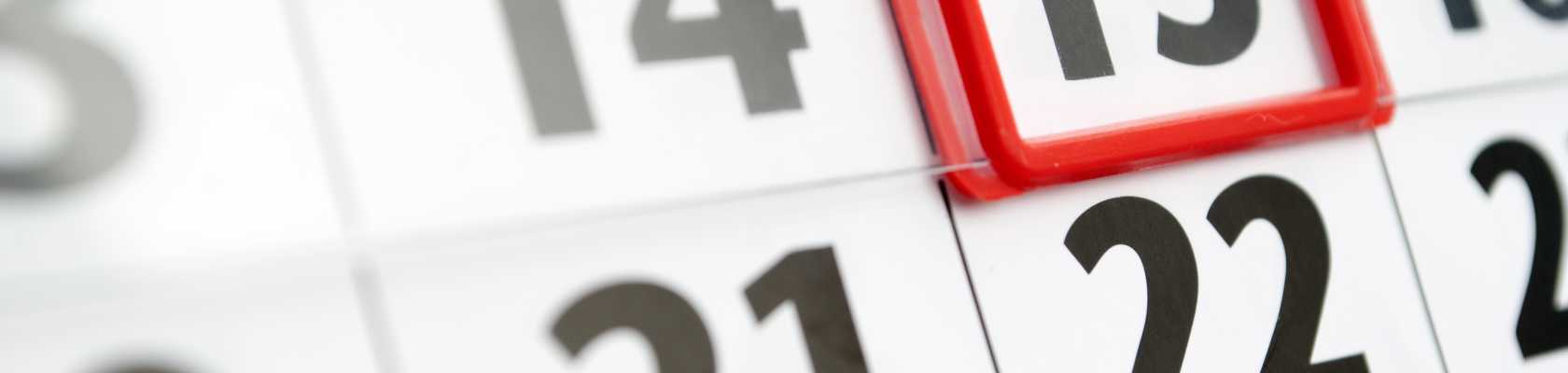
In part 1 of this series, we talked about setting up a system for maintenance scheduling, evaluating the system’s effectiveness, and ways to make it more efficient.
As you tweak your system to prioritize and schedule tasks, you’re going to want to find the best way to assign those tasks to your crew. Of course, this comes with its own set of nuances and challenges.
Ultimately, you want to match the workload with the workforce. Simple enough…at least in theory.
But how do you make theory practical? It’s all in the data.
Using Data to Balance Workload with Your Workforce
One of the key components of scheduling your crew is knowing how long each task takes and how many crew members are needed to do it.
If you’re just beginning to set up a system, this may require “guesstimating” and input from crew leaders. After all, some tasks are seasonal and don’t get done very often. Others may vary depending on conditions--like snow removal. Unless you have reports about the time, labor, and equipment requirements for each task you’re pretty much just making educated guesses.
And this could work for a while.
Eventually, however, those guesstimates will need to be backed up by records. Not just for effective crew scheduling, but also for cost tracking and asset management.
Your work order system is an excellent opportunity for crews or crew leaders to report back how long each ticket took as well as relaying other important information about the job.
If you are starting to develop a work order system or wondering how to improve an existing one, here are the components to consider:
- Types of maintenance work for your facilities. Inventory and categorize the necessary work needed throughout the year for each of your assets.
- Information needs for these tasks. Determine the data you need for staff scheduling, budget requests, managerial decisions, and equipment usage.
- How data is collected. Create a report form your team can use that provides all the necessary information for decision making.
- Appropriate training. Ensure your supervisory staff understands the data that needs to be collected. Allow inservice time so they can provide training for the rest of the crew.
- Testing and Refining. Not every system is going to work perfectly right off the bat. After a set period of time, evaluate your tracking system and make adjustments.
- Evaluating data. Data means nothing if it’s not being analyzed. How will the information you receive each month and check for patterns or unusual variations?
Collecting and Analyzing Data for Crew Scheduling
In the past, you may have a few crew leaders who could relay some of this information verbally or with written reports. That being said, they may not provide the exact details that will help with making future job scheduling more efficient.
Creating a form that crew leaders or department heads can fill out for each task or facility can help you collect the data you need. That data, however, needs to be added into a database for further interpretation.
Computerized maintenance tracking systems allow necessary staff to input information directly into a database. The resulting data provides insights into job scheduling, task analysis, cost tracking, asset maintenance, and more.
Once a computerized system is up and your staff is trained how to use it, the data becomes a huge asset for future planning.
The software then processes the data to give you a clear picture on how to approach your job scheduling, asset management, cost analysis, and much more.
Once a customized automated system is set up to collect and interpret data, scheduling requires much less time and mental bandwidth. Reports can easily be generated to help make decisions, analyze costs, and appease stakeholders.
In other words…it makes your job a lot easier.