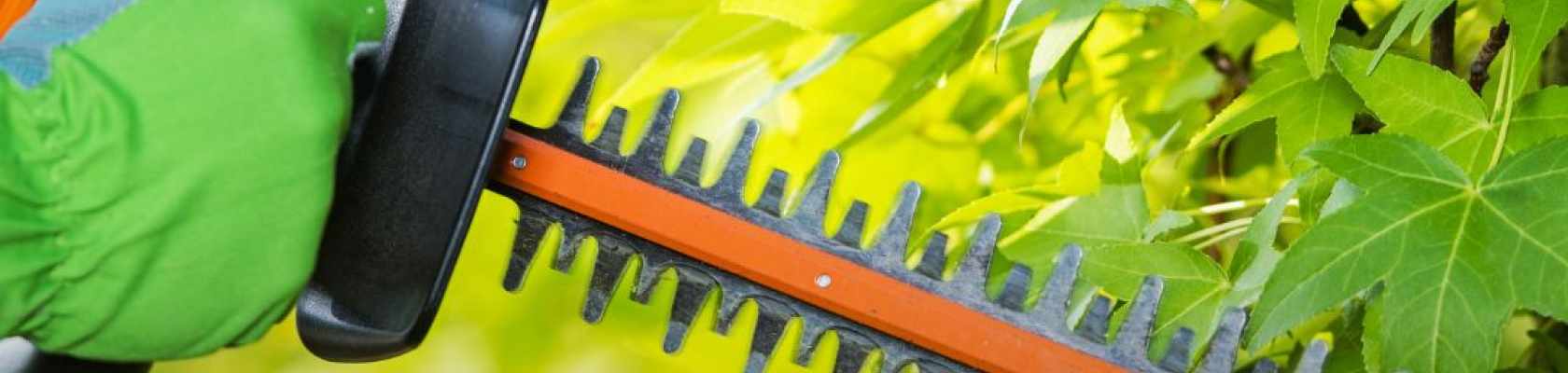
When it’s time to purchase new park maintenance equipment, you want to make sure you get your money’s worth. Finding the best equipment for park maintenance staff’s needs ensures they can get their jobs done safely and efficiently.
Misguided or hasty maintenance equipment choices can disrupt schedules with breakdowns and even lead to safety hazards. The growing season is a hectic time. Why make it more difficult with bad equipment?
Choosing park maintenance equipment can be more complex than simply visiting a big-box store. Processes are usually involved, and several things need to be considered when deciding on your purchase.
In this article, learn some of the things you may want to do before purchasing new park maintenance equipment.
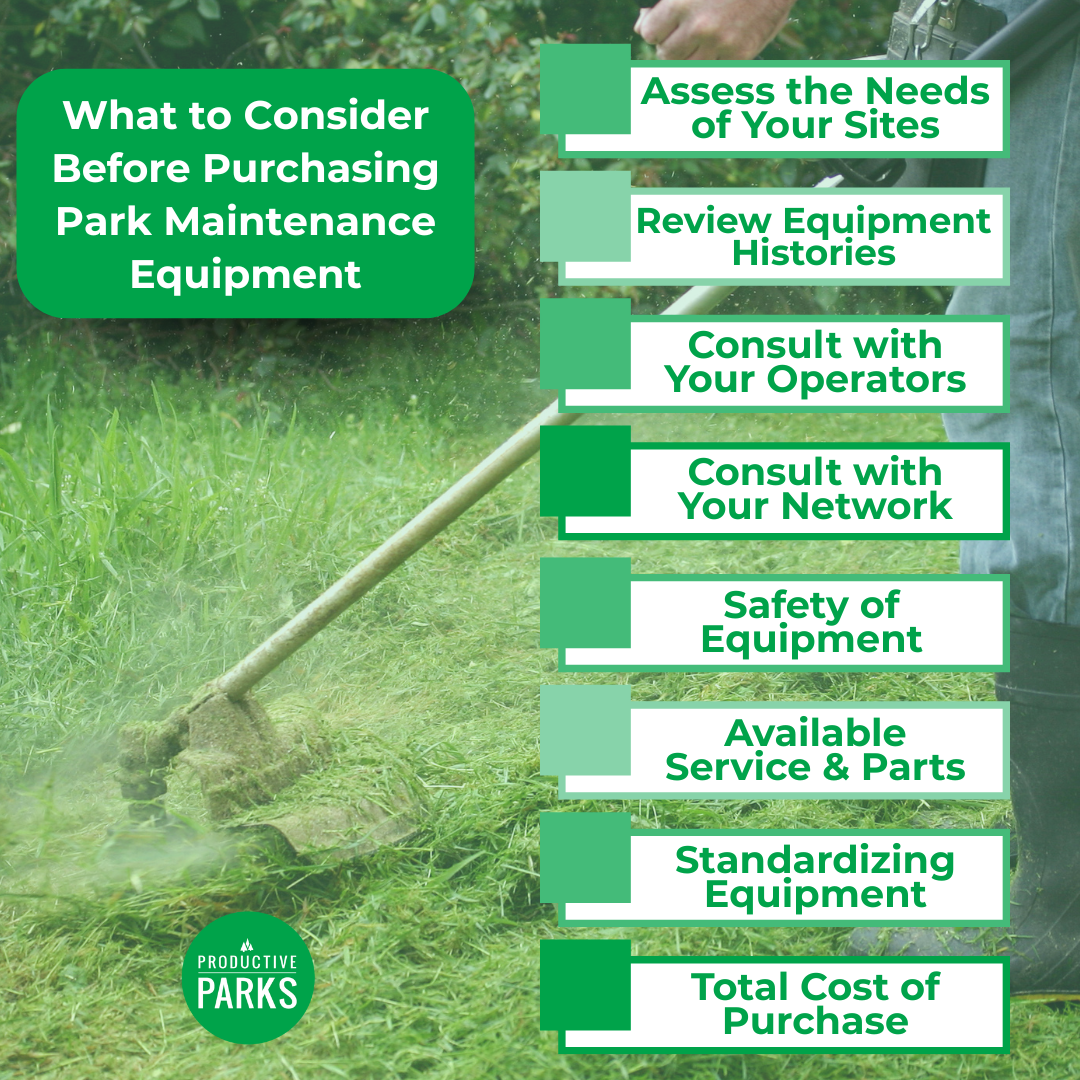
Assess the Needs of Your Sites
The type of equipment varies based on what you’re maintaining and how you’re caring for it.
Consider the size of the area you typically maintain, as well as any special concerns, such as uneven terrain, nearby water, and the types of vegetation present. What are the seasonal challenges of your assets, and what equipment do you need to handle it?
You want to ensure that the equipment you choose enables your team to complete their tasks with speed and efficiency. Determining what you need helps narrow down the “must-have” and “nice-to-have” features of your future equipment.
Once you determine the equipment with features that meet your needs, you can create a general list of options. The following things can help narrow down that list.
Review Equipment Histories
If your maintenance team keeps records about equipment usage, service history, and repairs, take some time to review the data.
Historical records can help the decision-making process by identifying the best-performing equipment brands and models your team uses.
Reviewing records also helps ensure you don’t repurchase equipment that isn’t a good fit for your maintenance needs.
If your current equipment records don’t provide the necessary information, consider implementing more effective asset management practices for both your existing and future equipment. A little extra work keeping records now can make decision-making much easier in the future.
Consult with Your Operators
Gathering input from individuals who use the equipment daily can also provide valuable insights. Their experience provides you with perspectives that you won’t find in sales brochures or online comparison articles.
You can analyze the equipment’s specs, price, and features from your office. Conversations with the maintenance team, however, can reveal some of the more intangible benefits.
For example, your park maintenance staff prefers a trimmer brand that is a little lighter and easier to handle. They say those little differences help them get work done faster, and it’s not so hard on the body when used for long periods. That brand of trimmer costs a little more, but the return on investment (ROI) comes quicker, with increased productivity and fewer injuries.
Consult with Your Network
Your parks and recreation network can also be an invaluable source of information. With a couple of phone calls or emails to other park maintenance managers, you can get answers to questions like:
- What equipment do similarly-sized agencies use?
- What challenges have they faced with the equipment they have?
- What brands and models are considered the best investment?
- Contact info for a great local sales rep.
Most park professionals are happy to “talk shop” and share what’s working for them. A good conversation can save time researching and the headaches from choosing the wrong maintenance equipment.
Safety of Equipment
You want to ensure the equipment operators can do their jobs safely. Inappropriate equipment can put them and those nearby in danger.
For example, if you have sites with larger trees that need occasional pruning and felling, you want to make sure the chainsaws you purchase are the correct size. Choosing a chainsaw that is too small because it is less expensive can mean the operator needs to make more cuts and passes from different angles, ultimately making the job take longer while compromising safety.
As equipment evolves, so do the safety features. Stay current on what safety features newer equipment has to offer. If your team struggles with incidents and injuries related to specific tasks, then try to find equipment that helps them complete these tasks more safely.
Availability of Service and Replacement Parts
Before you know it, that brand-new, shiny piece of equipment will need maintenance or repairs. Replacement parts will be required. It may need to be taken in for service. You have to know how readily available service and parts are for the brands and models you’re considering.
Can your maintenance team run to the local hardware store and get the parts they need to repair equipment? Is there a nearby service center? Will the equipment need to be shipped somewhere and likely be out of service for a period of time?
Equipment downtime disrupts your team’s maintenance plan. You want to ensure that you can minimize downtime when equipment breaks down.
Standardizing Your Equipment?
If there is a specific brand of equipment you and your team prefer, you may want to consider standardizing your equipment. The consistency of standardizing equipment can make it easier for your staff to operate and maintain. Your mechanics won’t need to learn how to fix different brands or stock as many different types of replacement parts. Plus, as equipment ages out, usable parts can be salvaged for other machines.
There are some drawbacks to sticking with one manufacturer for all your equipment. First, a single manufacturer may not make all the equipment that best suits your team's needs. For example, your landscaping team may prefer one brand of mower but a different brand of edger. Also, if you’re locked into one manufacturer, your team may not be aware of the innovations and features coming out from other equipment brands.
Total Overall Cost
Once you have narrowed down your search to a couple of makes and models, now is the time to factor in the overall cost, including shipping, training, warranties, service plans, and various other “soft costs.”
From there, you should be very close to making an informed decision about the park maintenance equipment your team will use.
The Takeaway
Spending some extra time researching and engaging in conversations can help you find the best park maintenance equipment that suits your budget and staff’s needs. Reviewing historical records, consulting with industry experts, and understanding how equipment will be maintained all play crucial roles in selecting the best equipment.