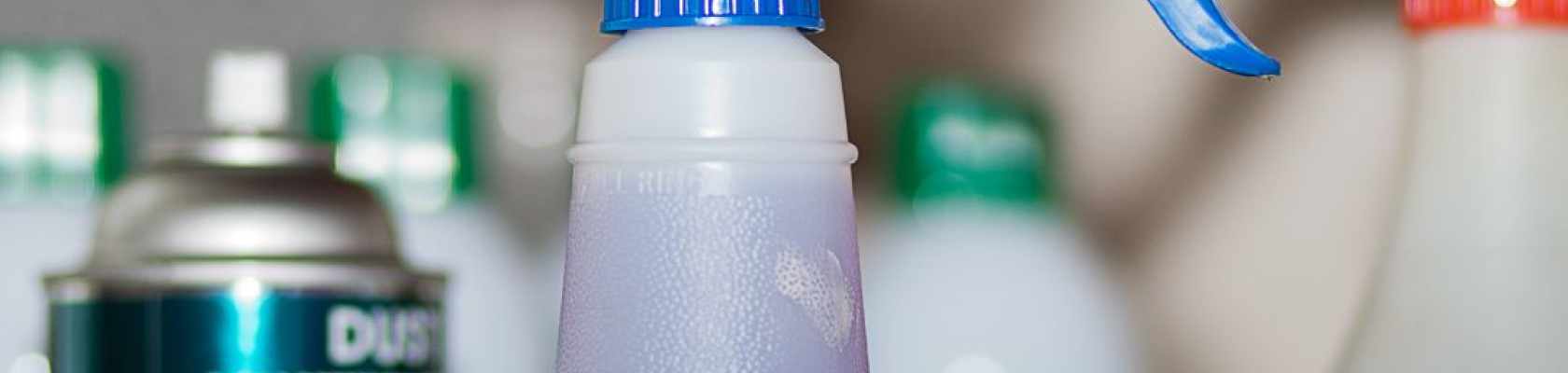
We often take our inventory for granted until we unexpectedly run out of something at the worst possible time. Or someone accidentally overorders something, and there is no place to store it.
Inventory management is essential for running a maintenance department. Without it, storage cabinets and closets become a mystery, stock disappears, and ordering is inaccurate.
But inventory often gets overlooked when things get busy, or you’re dealing with a string of unexpected repairs.
Luckily, there are some things you can do to maintain better inventory.
In this article, get some tips on effective inventory management. Then, see how technology like maintenance inventory management software can help make the process even easier.
What is Maintenance Inventory Management?
Maintenance inventory management involves finding the most cost-effective way to get the right stock in the right place when needed. It includes thoroughly understanding what is in your storage spaces, how much more you need, and the best time to order.
Inventory management also includes auditing inventory levels, setting ordering thresholds, and planning for the unexpected. For parks and recreation agencies, managing inventory also varies based on seasonal needs.
Understanding all these aspects of inventory management gives your maintenance team what they need to manage the agency’s assets effectively.
Tips for Managing Inventory
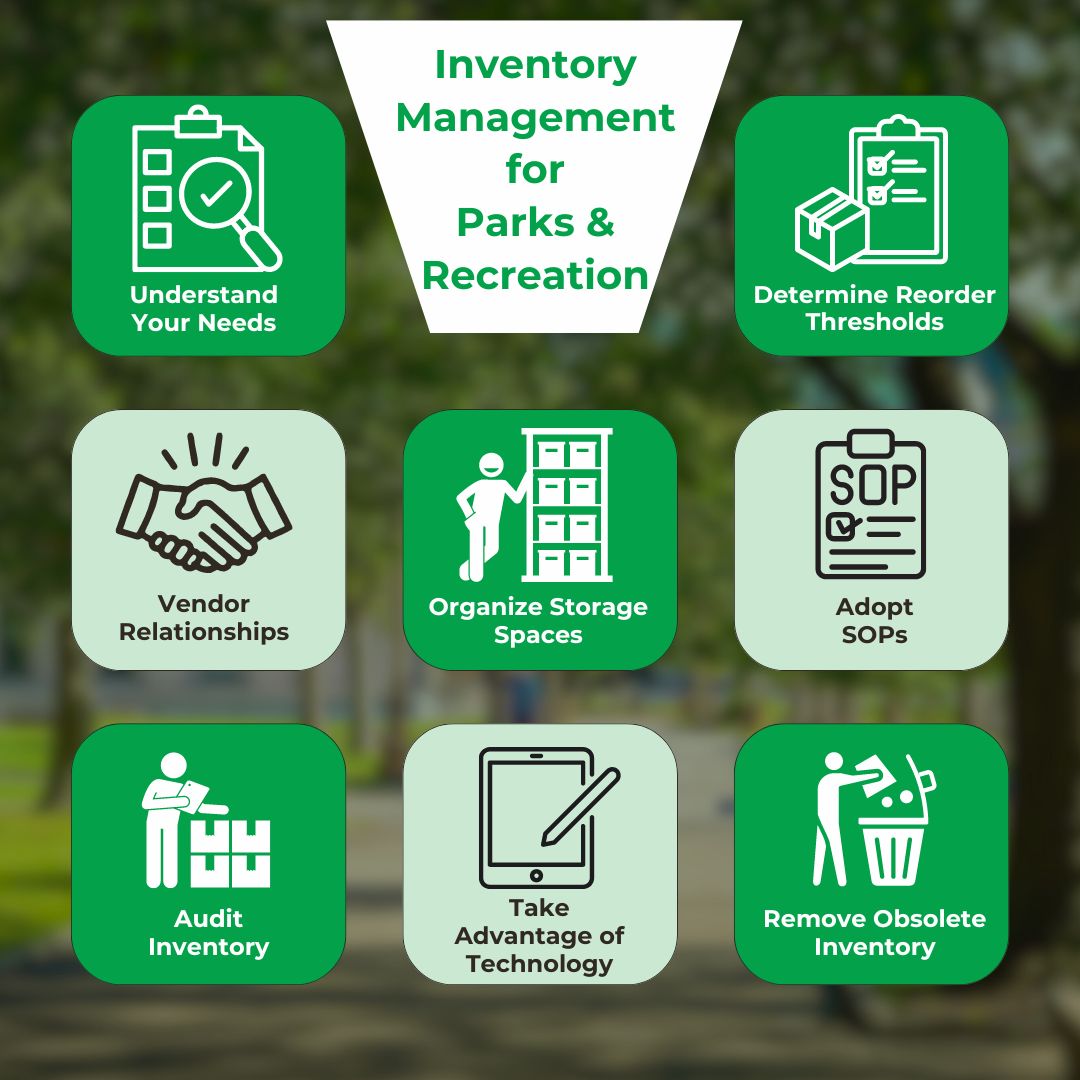
Inventory management can be complicated, especially with all the assets parks and recreation agencies manage. Here are some good places to begin:
Understand Your Varying Needs
A park maintenance team’s inventory needs often fluctuate with the seasons. For example, during the growing season, the team will need more herbicides, replacement parts for landscaping equipment, and garbage bags for outdoor waste receptacles. In the winter, inventory purchasing may shift to ice melt, indoor cleaning supplies, and other facility needs.
Special events can also quickly deplete standard supplies. Knowing what is coming up and the required inventory allows staff to order proactively for activities and events.
Using historical records from past events allows inventory managers to create more accurate orders.
Determine Your Reorder Thresholds
While determining your needs, you should also consider how low your stock can go before reordering. Your reorder thresholds will vary based on demand for inventory, turnaround times on orders, and available space.
Ideally, you will have historical records to help determine stock usage and the delivery lead time. That way, you can avoid stockouts, overstock, and paying extra for expedited shipping.
You may need to adjust your thresholds based on the seasons to ensure your inventory keeps up with maintenance tasks and programming.
Maintain Relationships with Vendors
It never hurts to have a good relationship with your vendors. For example, if you have a big event coming up in a couple of months, contacting your vendor about your increased need for supplies allows you to get them when they need them while ordering them at lower prices.
Your vendor may alert you when they have specials or promotions on supplies you use. That way, if you have the space, you can get more for your budget dollars.
Keep Organized Storage Spaces
Disorganized storage makes inventory management almost impossible. How can you know what you have if you don’t know where to find it?
Develop a method of organization that makes the most sense to your team. Depending on your workflows and available storage, you may group by assets, types of products, or what gets used by different divisions of the maintenance department.
Have Standard Operating Procedures for Using Inventory
Does your staff clearly understand how to report the supplies and materials they use while completing maintenance tasks?
Some agencies opt for a sign-in/sign-out process or one point of contact to pull supplies from storage. Other agencies use spreadsheets or maintenance software to help track what gets used.
Part of maintenance staff onboarding should include a section on inventory management. Storage areas should also have clear directions about adding or using inventory. Whatever methods track inventory, all your staff need to know how to do it.
Audit Your Inventory
At some point, you want to be able to determine whether what you think you have is what you actually have. This is true whether you use inventory software, spreadsheets, or paper records.
We’ve all seen discrepancies between our perceived inventory and what’s on the shelf. Staff don’t report what they use, sometimes it “grows legs,” and other times it’s not being tracked accurately.
Whatever the reason, auditing your inventory helps ensure you have what you think you have, your supply forecasting is accurate, and nothing is stored that doesn’t need to be.
Remove Obsolete Inventory
As your assets change, so will your inventory needs. For example, you may need a whole new series of replacement parts when you upgrade your mowers or vehicles. Those obsolete replacement parts will take up precious storage real estate until your next inventory audit.
When you replace old equipment or assets, determine what related inventory will no longer be useful and remove it as soon as possible. Ensuring only the most current, relevant inventory is stocked helps prevent any errors or misunderstandings related to outdated inventory.
Technology to Manage Maintenance
A maintenance inventory system is software that helps agencies track and manage their replacement parts, consumables, supplies, and personal protective equipment. This type of software can be standalone or part of a suite of features found in computerized maintenance management system (CMMS) software.
The ultimate goal of inventory management software is to make your job easier. By providing dashboards about the quantity and locations of your stock, you know what you have without needing to go through storage closets. You can also receive alerts when stock reaches a threshold level.
Data from inventory management software can also help you understand where your inventory budget is going and what is being used when, which will help you forecast and order more accurately.
The Takeaway
Managing inventory is a delicate balance among all the other hats a maintenance manager needs to wear. Understanding your inventory stock and usage, however, will make operations go much smoother because you will have the right supplies or parts when you need them.
Processes and technology can help ensure your stockrooms are filled with what your team needs. By paying attention to previous records about tasks, events, preventative maintenance, and seasonal ordering, you can order more confidently.